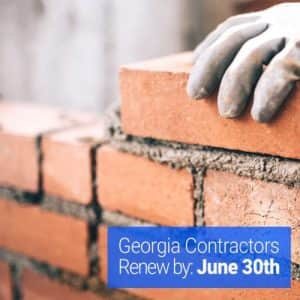
Steps to Renew a Contractor's Business License in Georgia
Published on September 3, 2024 by Alicia Eckert
An applicant for renewal of his or her residential license must have completed 3 hours of acceptable continuing education each year for a Georgia Residential Basic license and 6 hours of continuing education each year for a Georgia Residential Light Commercial license, with a year being July 1st through June 30th.